“With our ‘design for environment’ approach, we are devising our vehicles to be as resource-efficient and environmentally friendly as possible throughout their entire life cycle,” said Klaus Ruhland from Group Environmental Protection, explaining how Mercedes-Benz takes sustainability into account already during product development. The topic of sustainability is embedded as a basic guiding principle in the strategy of the carmaker. With the transformation from “electric first” to “electric only,” the brand with the star aims to become all-electric by the end of the decade – wherever market conditions allow. With Ambition 2039, the company is at the same time advancing concrete measures to make its entire fleet of Mercedes-Benz passenger cars and vans carbon-neutral along the entire value chain and over the entire life cycle by 2039 – much earlier than required by the EU.
The Mercedes-Benz EQS delivers sustainability
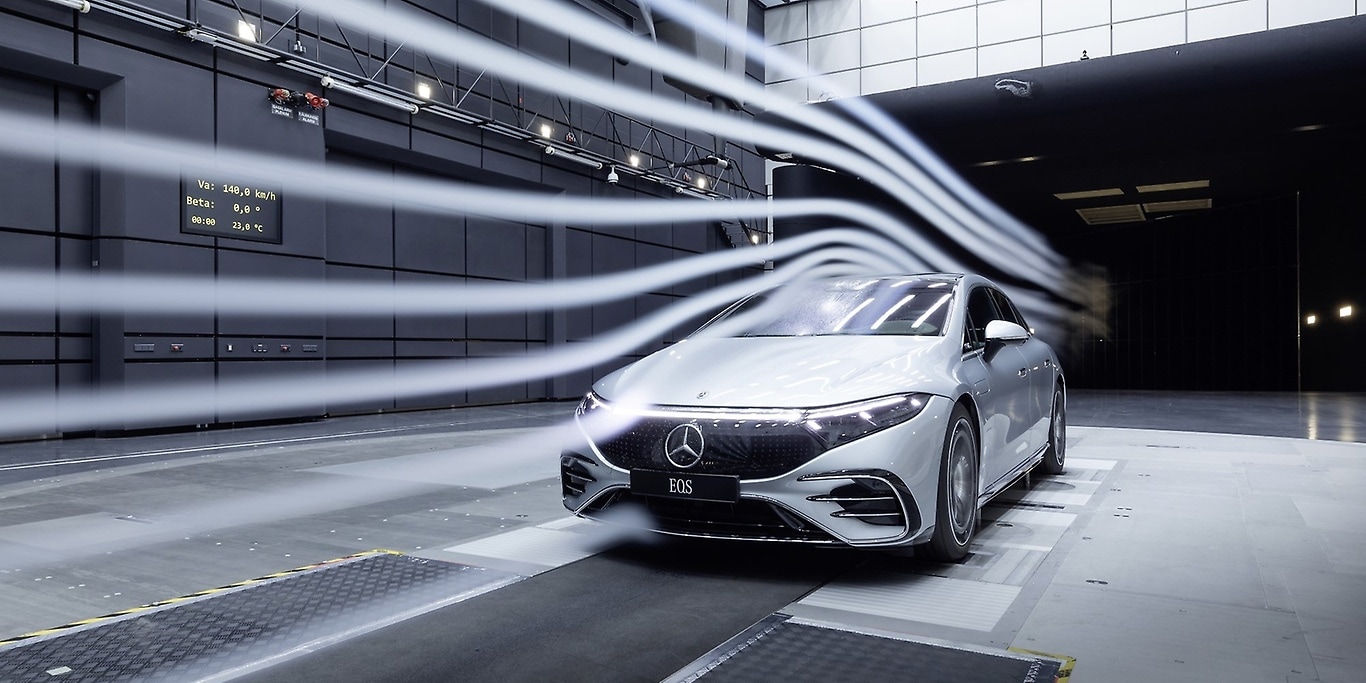
In the circle.
The only desirable luxury is sustainable luxury. Mercedes-Benz is therefore emphasising sustainability even in the product development phase. From the battery to the carpet –the new Mercedes-Benz EQS is putting real solutions for zero-emission mobility, intelligent resource-conserving features, and a responsible circular economy concept on the road.
12 min reading time
Content
- Intelligent reduction of resource consumption
- Pioneering spirit for sustainable product development
- Supply chain from the mine to recycling
- Carbon-neutral production
- Long battery life conserves resources
- Two lives for the energy transition
- Recycling is part of the development
- Green steel starting in 2025
- Green charging with sustainability and transparency for the customer
Intelligent reduction of resource consumption
“The circular economy is an important component in achieving the target,” Ruhland said. “Mercedes-Benz has set a target for itself to increase the share of secondary raw materials used in its passenger car fleet to an average of 40 percent by 2030.” The Mercedes-Benz EQS (Electrical consumption in kWh/100 km (combined): 19.6-16.2; CO₂ emissions in g/km (combined): 0)¹. demonstrates how this philosophy is becoming reality. In the electric flagship from the luxury limousine segment, intelligent resource efficiency and a minimised carbon footprint demonstrate how sustainability is implemented at Mercedes-Benz.
Recycled plastic is already being used in larger components like wheel arch or underbody panels as well as many small parts like pushbuttons, plastic nuts and cable fasteners. The components in the EQS, which are manufactured resource-efficiently using recycled and renewable raw materials, already weigh more than 80 kilograms. The floor coverings are made of regenerated nylon. One ton of this innovative yarn saves more than 6.5 tons of carbon compared to virgin material.
Pioneering spirit for sustainable product development
Developments like these are no coincidence. Quite the contrary. Throughout the company, a pioneering spirit infuses the research into sustainable product development. The “leather” of the future is created at Future Inside Systems in Böblingen, which is headed by Daniel Fuhrmann, who is involved in with future technologies for a sustainable vehicle interior. “Materials made from bacterial nanocellulose or based on fungal mycelia can have the look and feel of leather. But they are much more resource-efficient to produce, are animal-free, and are biodegradable.” He said that if material tests go well, the synthetic leather made from bacterial cellulose could be used in the future not only for seat covers but also for laminated surfaces like door panels and instrument panels.
From basic research to implementation in series production, the Future Outside & Materials team is also driving innovations for a sustainable exterior. “High-quality upcycling is becoming a trend in materials development for components in the automotive industry,” said team Head Karl-Heinz Füller. In other words, used materials will be made into new, highly advanced components. One example are the high-tech insulation mats for the S-Class, which incorporate previously unusable textile scraps from used tires. At the same time, the team is developing other imaginative solutions and wants to use pyrolysis to convert plastic waste back into recyclable oil in a field test.
Supply chain from the mine to recycling
Battery cells for the EQS are an important step on the road to carbon neutrality: “Suppliers produce the battery cells in a carbon-neutral process. This means that total emissions from cell production can be reduced by about 30 percent,” says Ruhland. The high-performance cell chemistry contains nickel, cobalt and manganese in a ratio of 8:1:1. This has already cut the cobalt content to about ten percent. “Ecologically, the reduction of the cobalt content in battery cells is an enormous advancement,” Ruhland stressed. When considering the entire supply chain from mine to recycling, special focus is also placed on respect for human rights in the working conditions for employees throughout the entire supply chain – in future, Mercedes-Benz will also only be sourcing cobalt and lithium from certified mining operations.
Carbon-neutral production
The battery system of the EQS will soon be assembled in a carbon-neutral process in the Hedelfingen plant section of the Untertürkheim site and delivered to the state-of-the-art Factory 56 in Sindelfingen for installation in the EQS. As the car factory of the future, Factory 56 in Sindelfingen manufactures flexibly, digitally, efficiently, ergonomically – and above all, sustainably. Factory 56 was designed from the start to be carbon-neutral and thus is a zero-carbon manufacturing plant. For example, it draws energy for its power supply entirely from renewable resources. The photovoltaic system installed on the factory roof alone supplies up to 30 percent of the production hall’s total annual consumption. Excess solar power also flows into a connected stationary energy storage system. Following Factory 56, all of the company’s own Mercedes-Benz passenger car and battery assembly plants will be converted to climate-neutral production by 2022.
Accusations that the climate footprint of an e-car is hopelessly overburdened by the battery alone have already been sufficiently refuted by multiple studies. The tenor of all of the studies by the Fraunhofer Institute, the Greens in the Bundestag and the Federal Environment Ministry: Even with the current electricity mix, electric cars have a climate advantage over gasoline or diesel vehicles over their entire service life. The carbon footprint of the EQS – if it is consistently charged with green electricity – is actually 80 percent better over its entire lifecycle than that of a combustion engine. The higher emissions from the manufacture of the EQS when compared with a conventional S-Class will have been recouped after just 20,000 kilometres. Incidentally, the carbon footprint of both cars will soon be zero.
Long battery life conserves resources
One decisive factor in conserving resources is achieving the longest possible service life. The battery is a good example of this: once the high-voltage battery has been connected in Factory 56 and the EQS has been brought to life for the first time with the start button, the battery certificate is valid for up to ten years or for mileage of up to 250,000 kilometres. The option of over-the-air updates also ensures that the energy management system can always be updated to the latest state of technology over the entire life of the vehicle.
Remanufacturing plays an important role in the sustainability strategy of Mercedes-Benz. With this process, called “Reman” for short, the service life of batteries in the vehicle can be extended. As part of the process, for example, cells that are no longer functional are replaced with new ones. Mercedes-Benz has been working on this industrial process, in which batteries are dismantled, refurbished and again made fit for use in e-cars, since 2010. All in keeping with the high quality standards of Mercedes-Benz and with its own patents, of course. Around 95 percent of a defective energy storage unit can be prepared for continued used in this way. Mercedes-Benz offers Reman batteries for all current electric vehicles, thus making an important contribution to resource conservation and the concept of a closed economic cycle in after-sales as well. This enables the company to offer customers access to reconditioned batteries.
Two lives for the energy transition
And even when the natural chemical process of capacity decrease excludes further use as a traction battery, a lithium-ion battery can still perform a valuable service in its second life as an energy storage device. This is where Mercedes-Benz Energy GmbH, a subsidiary of Mercedes-Benz, comes in. “With Mercedes-Benz Energy, we have established a successful business model with stationary large-scale storage applications. Maximising the potential of a battery by extending its life cycle in the form of a second-life energy storage unit is our goal here. In this way, we not only increase your economic benefit. The extended use phase at the same time improves the environmental footprint of the batteries, since the valuable raw materials remain in the cycle,” said Gordon Gassmann, Managing Director of Mercedes-Benz Energy, explaining the far-reaching impact of the company’s sustainable strategy. Batteries that can no longer be used in vehicles continue to be used in second-life applications. Storage systems like these contribute to the energy transition in important ways, such as by absorbing or releasing electricity from the public grid in just fractions of a second. By doing so, they ensure grid stability by compensating for overvoltage or undervoltage caused by fluctuating renewable sources such as the wind or sun.
Recycling is part of the development
At some point, the definitive end of the road comes for every battery. This is when the value of a sustainability strategy with a complete recycling concept for all vehicle components becomes clear. All components and materials are already analysed during the development phase for their suitability as parts of a circular economy. As a result, 85 percent of the materials in all Mercedes-Benz passenger car models is recyclable. A total of 95 percent of a vehicle is recyclable at the end of its life cycle. “With the circular economy of battery systems in mind, we are pursuing a holistic approach with three core themes: circular design, value retention and closing the loop,” said environmental expert Ruhland. “Material recycling of the valuable raw materials used like lithium, nickel, manganese and cobalt, is a precondition for a sustainable business model for the electric mobility of the future.” Regarding the mileage of electric vehicles, significant quantities of batteries for recycling are not expected until the 2030s. Mercedes-Benz intends to use the time until then for developing and securing its own know-how for the recycling process of the precious materials. The company is currently evaluating and planning the construction of a battery recycling factory in Kuppenheim, Germany. Production could start as early as 2023 – depending on talks with the authorities.
Green steel starting in 2025
Which raw materials in the finished car will have the biggest impact in terms of sustainability? Aside from batteries, these are steel, aluminium and plastics. As part of Ambition 2039, Mercedes-Benz is already engaging with these materials and components, which are particularly environmentally relevant in production and processing, with special emphasis in development and procurement. Together with its steel suppliers, Mercedes-Benz is pursuing the goal of a green steel supply chain. “We are intentionally focusing not on offsetting but rather on avoiding and reducing emissions,” emphasised steel purchasing agent Andre Joao Teixeira Lameira.
The steel processed for the EQS at the Mercedes-Benz pressing plants consists largely of recycled steel scrap. In the traditional blast furnace route, the production of one ton of steel produces an average of more than two tons of CO₂. These emissions are cut by more than 60 percent in the case of flat steel from Salzgitter AG, which consists entirely of recycled steel scrap. At Big River Steel, a U.S. steel supplier to Mercedes-Benz, the use of steel scrap and renewable energies reduces carbon emissions in steel production by more than 70 percent. The supplier was presented this year with Daimler Sustainability Recognition, a sustainability award for suppliers.
The Swedish start-up H2 Green Steel, in which Mercedes-Benz is the first passenger car manufacturer to participate for the use of carbon-free steel in series production vehicles
Green charging with sustainability and transparency for the customer
Mercedes-Benz is already effectively reducing climate-relevant emissions and the consumption of natural resources with many measures in development, purchasing and production. But production only makes up about half of the carbon footprint of a battery electric vehicle. The other half accrues in the use phase – if the current EU electricity mix and its emissions are taken as a basis. Electricity from renewable energies, preferably from home photovoltaic systems, is therefore a significant factor in avoiding carbon emissions in the life cycle of an electric car.
This is why, since March 2021, Mercedes-Benz has been enabling customers of all Mercedes EQ and plug-in hybrid models to charge at more than 200,000 public charging points in Europe via Mercedes me Charge. Green charging as an integral part of Mercedes me Charge ensures the use of energy from renewable resources. Guarantees of origin ensure that an equivalent amount of electricity from renewable energies is fed into the power grid for the charging processes. The launch of “green charging” in the U.S. and Canada followed with the EQS in August 2021. So the turn signal has already been set in the all-electric luxury limousine from Mercedes-Benz – in the direction of the recycling loop and a carbon-neutral future.
¹ Data on electricity consumption are provisional and have been determined internally in accordance with the NEDC test methods certification method. So far, there are neither confirmed values from TÜV nor an EC type approval nor a certificate of conformity with official values. Deviations between the data and the official values are possible.