„Mit dem Ansatz ‚Design for Environment‘ konzipieren wir unsere Fahrzeuge so, dass sie im gesamten Lebenszyklus möglichst ressourcenschonend und umweltfreundlich sind“, erklärt Klaus Ruhland vom Konzern-Umweltschutz, wie Mercedes-Benz Nachhaltigkeit bereits bei der Produktentwicklung mitdenkt. Denn das Thema Nachhaltigkeit ist in der Strategie des Automobilbauers als grundlegendes Leitprinzip verankert. Mit der Transformation von „Electric first“ zu „Electric only“ will die Marke mit dem Stern bis zum Ende des Jahrzehnts vollelektrisch werden – überall dort, wo es die Marktbedingungen zulassen. Gleichzeitig forciert das Unternehmen mit der Ambition 2039 konkrete Maßnahmen, um die komplette Mercedes-Benz Pkw- und Van-Neuwagenflotte entlang der gesamten Wertschöpfungskette und über den gesamten Lebenszyklus bis 2039 CO₂-neutral zu stellen – und das deutlich früher als von der EU gefordert.
So nachhaltig ist der Mercedes-Benz EQS
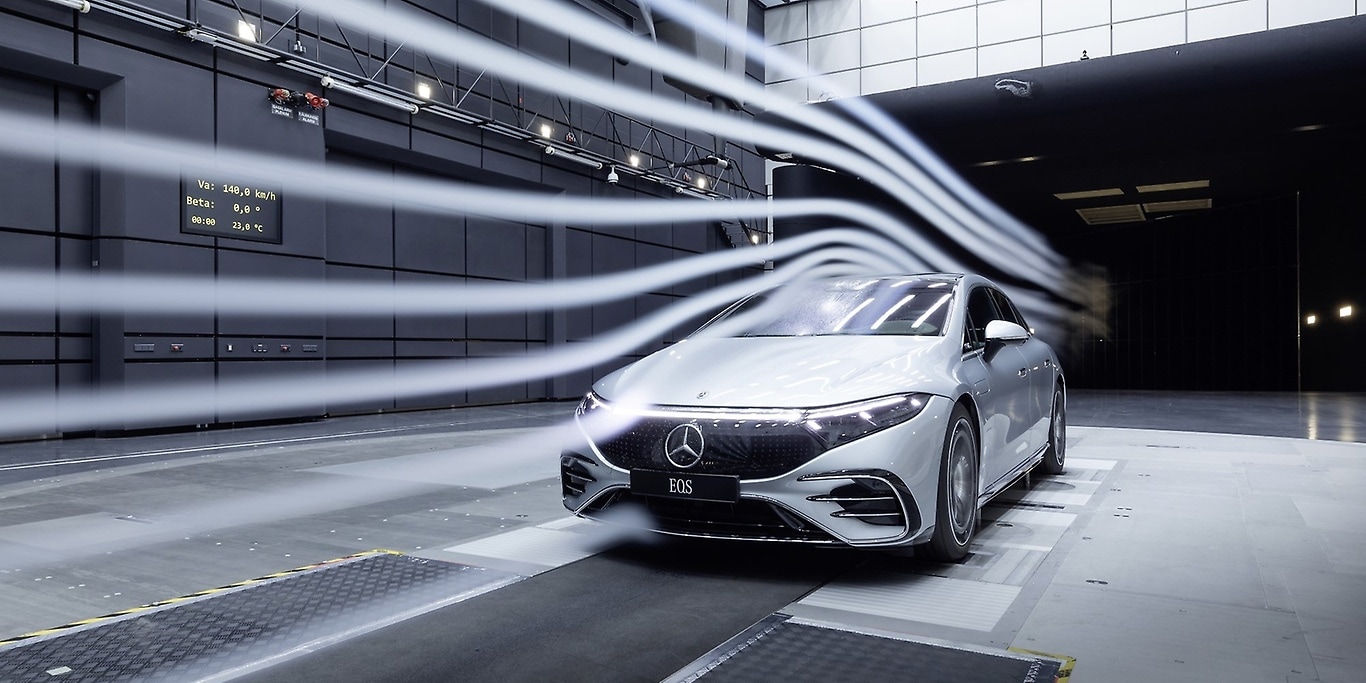
Im Kreislauf.
Nur nachhaltiger Luxus ist auch erstrebenswerter Luxus. Deshalb treibt Mercedes-Benz Nachhaltigkeit bereits in der Produktentwicklung voran. Von der Batterie bis zum Teppich bringt der neue Mercedes-Benz EQS reale Lösungen für emissionsfreie Mobilität, intelligente Ressourcenschonung und verantwortungsvolle Kreislaufwirtschaft auf die Straße.
12 Min. Lesedauer
Inhalt
- Intelligente Ressourcenschonung
- Pioniergeist für nachhaltige Produktentwicklung
- Lieferkette von der Mine bis zum Recycling
- CO₂-neutrale Produktion
- Langes Batterieleben schont Ressourcen
- Zwei Leben für die Energiewende
- Recycling ist Teil der Entwicklung
- Grüner Stahl ab 2025
- Grünes Laden mit Nachhaltigkeit und Transparenz für die Kunden
Intelligente Ressourcenschonung
„Eine wichtige Komponente bei der Zielerreichung ist die Kreislaufwirtschaft“, so Ruhland. „Mercedes-Benz hat sich zum Ziel gesetzt, bis 2030 den Anteil von Sekundärrohstoffen für die Pkw-Flotte auf durchschnittlich 40 Prozent zu erhöhen.“ Wie diese Philosophie Realität wird, zeigt der Mercedes-Benz EQS (Stromverbrauch in kWh/100 km (kombiniert): 19,6-16,2; CO₂-Emissionen in g/km (kombiniert): 0)¹. Im elektrischen Flaggschiff aus dem Segment der Luxuslimousinen stehen intelligente Ressourcenschonung und ein minimierter CO₂-Fußabdruck beispielhaft für die Umsetzung von Nachhaltigkeit bei Mercedes-Benz.
Bereits heute enthalten größere Bauteile wie beispielsweise Radlauf- oder Unterbodenverkleidungen und viele Kleinteile wie Druckknöpfe, Kunststoffmuttern und Leitungsbefestiger wiederverwerteten Kunststoff. Im EQS wiegen die Bauteile, die ressourcenschonend unter Verwendung von Rezyklaten und nachwachsenden Rohstoffen hergestellt sind, bereits über 80 Kilogramm. Die Bodenbeläge sind aus regeneriertem Nylon hergestellt. Eine Tonne dieses neuartigen Garns spart über 6,5 Tonnen CO₂ im Vergleich zu Neuware.
Pioniergeist für nachhaltige Produktentwicklung
Solche Entwicklungen sind kein Zufall. Im Gegenteil. Im gesamten Unternehmen wird mit Pioniergeist an nachhaltigen Produktentwicklungen geforscht. Das „Leder“ der Zukunft entsteht bei Daniel Fuhrmann, der sich in Böblingen als Leiter „Future Inside Systems“ unter anderem mit Zukunftstechnologien für ein nachhaltiges Fahrzeuginterieur befasst. „Materialien aus bakterieller Nano-Zellulose oder auf Basis von Pilzmyzelien können die Optik und Haptik von Leder haben. Sie sind aber wesentlich ressourcenschonender in der Herstellung, tierfrei und biologisch abbaubar.“ Der Lederersatz aus bakterieller Zellulose lasse sich, wenn die Materialtests gut verlaufen, künftig nicht nur für Sitzbezüge, sondern auch für kaschierte Oberflächen wie Türverkleidungen oder Instrumententafeln verwenden.
Von der Grundlagenforschung bis zur Umsetzung in der Serie treibt auch das Team „Future Outside & Materials“ Innovationen für ein nachhaltiges Exterieur voran. „Qualitativ hochwertiges Upcycling wird ein Trend in der Werkstoffentwicklung für Bauteile in der Automobilindustrie werden“, weiß Leiter Karl-Heinz Füller. Heißt: Gebrauchte Werkstoffe werden zu neuen anspruchsvollen Bauteilen. So wie Hightech-Dämmungsmatten der S-Klasse, in denen bisher nicht verwertbare Textilresten aus Altreifen verarbeitet sind. Gleichzeitig denkt das Team über den Tellerrand hinaus und will in einem Betriebsversuch durch Pyrolyse Plastikmüll in wiederverwertbares Öl zurückverwandeln.
Lieferkette von der Mine bis zum Recycling
Die Batteriezellen für den EQS sind ein wichtiger Schritt auf dem Weg zur CO₂-Neutralität: „Die Lieferanten produzieren die Batteriezellen CO₂-neutral. Damit können die gesamten Emissionen der Zellfertigung um etwa 30 Prozent vermindert werden.“ so Ruhland. Die performante Zellchemie enthält Nickel, Kobalt und Mangan im Verhältnis 8:1:1. Dadurch reduziert sich der Kobaltgehalt bereits heute auf rund zehn Prozent. „Ökologisch ist die Reduktion des Kobaltanteils in den Batteriezellen ein enormer Fortschritt“, betont Ruhland. Bei der Betrachtung der gesamten Lieferkette von der Mine bis zum Recycling liegt auch ein hohes Augenmerk auf der Einhaltung der Menschenrechte bei den Arbeitsbedingungen der Beschäftigten über die die gesamte Lieferkette: Künftig wird Mercedes-Benz Kobalt und Lithium zudem nur noch aus zertifiziertem Abbau beziehen.
CO₂-neutrale Produktion
Das Batteriesystem des EQS wird im Untertürkheimer Werkteil Hedelfingen schon in Kürze CO₂-neutral montiert und in die hochmoderne Factory 56 in Sindelfingen zum Einbau in den EQS zugeliefert. Die Factory 56 in Sindelfingen als Autofabrik der Zukunft fertigt flexibel, digitalisiert, effizient, ergonomisch – und vor allem nachhaltig. Die Factory 56 wurde von Beginn an CO₂-neutral und damit als Zero Carbon Fabrik konzipiert. Dabeie bezieht sie beispielsweise ihre Energie zur Stromversorgung komplett aus erneuerbaren Ressourcen. Allein die auf dem Dach der Fabrik installierte Photovoltaikanlage deckt jährlich bis zu 30 Prozent des Gesamtverbrauchs der Halle ab. Überschüssiger Solarstrom fließt zudem in einen angekoppelten stationären Energiespeicher. Nach der Factory 56 werden ab 2022 alle eigenen Mercedes-Benz Pkw- und Batteriemontagestandorte auf klimaneutrale Produktion umgestellt sein.
Vorwürfe, wonach die Klimabilanz eines E-Autos durch die Batterie chancenlos vorbelastet ist, wurden bereits in mehreren Untersuchungen hinlänglich widerlegt. Tenor aller Studien vom Fraunhofer Institut, den Grünen im Bundestag oder auch dem Bundesumweltministerium: E-Autos haben schon mit dem heutigen Strommix über die gesamte Lebensdauer einen Klimavorteil gegenüber Benzin- oder Dieselfahrzeugen. Im Vergleich zum Verbrenner ist beim EQS die CO₂-Bilanz über den gesamten Lifecycle sogar um 80 Prozent besser – wenn konsequent mit Grünstrom geladen wird. Bereits nach 20.000 Kilometer haben sich dann die höheren Emissionen aus der Herstellung des EQS gegenüber einer konventionellen S-Klasse amortisiert. In der Klimabilanz der Montage steht bei beiden in Kürze übrigens eine Null.
Langes Batterieleben schont Ressourcen
Ein ausschlaggebender Faktor beim Schutz der Ressourcen ist die möglichst lange Lebensdauer. Die Batterie ist dafür ein gutes Beispiel: Nachdem der Hochvolt-Akku in der Factory 56 verkabelt ist und der EQS mit dem Startknopf zum ersten Mal zum Leben erweckt wurde, gilt das Batteriezertifikat bis zu einer Laufzeit von zehn Jahren oder bis zu einer Laufleistung von 250.000 Kilometern. Die Möglichkeit von Over-the-Air-Updates stellt zudem sicher, dass das Energiemanagement über die gesamte Lebensdauer des Fahrzeugs immer wieder auf den neuesten Stand der Technik gebracht werden kann.
Remanufacturing spielt in der Nachhaltigkeitsstrategie von Mercedes-Benz eine wichtige Rolle. Mit dem kurz Reman genannten Verfahren lässt sich die Lebensdauer von Batterien im Fahrzeug verlängern. Dabei werden beispielsweise nicht mehr funktionstüchtige Zellen durch neue ersetzt. Bereits seit 2010 arbeitet Mercedes-Benz an diesem Prozess, in dem Akkus demontiert und in einem industriellen Verfahren für den erneuten Einsatz im E-Auto fit gemacht werden. Selbstverständlich nach den hohen Mercedes-Benz Qualitätsstandards und mit eigenen Patenten. Rund 95 Prozent eines defekten Energiespeichers lassen sich so weiter nutzen. Mercedes-Benz bietet für alle aktuellen elektrischen Fahrzeuge Reman-Batterien an und leistet damit auch im After-Sales einen wichtigen Baustein zur Ressourcen-Schonung und zum Gedanken eines geschlossenen Wirtschaftskreislaufes.
Zwei Leben für die Energiewende
Und selbst dann, wenn der natürliche chemische Prozess der Kapazitätsminderung die weitere Verwendung als Fahrbatterie ausschließt, leistet ein Lithium-Ionen-Akku in seinem zweiten Leben in Form eines Energiespeichers noch wertvolle Dienste. Genau hier setzt die Mercedes-Benz Energy GmbH als Tochterunternehmen von Mercedes-Benz an. „Wir haben mit der Mercedes-Benz Energy ein erfolgreiches Geschäftsmodell mit stationären Großspeicheranwendungen etabliert. Das Potenzial einer Batterie maximal auszunutzen indem man ihren Lebenszyklus in Form eines 2nd-Life-Energiespeichers verlängert, ist dabei unser Ziel. Damit steigern wir nicht nur Ihren wirtschaftlichen Nutzen. Gleichzeitig verbessert die verlängerte Nutzungsphase die Ökobilanz der Akkus, denn die wertvollen Rohstoffe bleiben weiterhin im Kreislauf.“, erklärt Gordon Gassmann, Geschäftsführer der Mercedes-Benz Energy die weitreichende Wirkung der nachhaltigen Unternehmensstrategie. Batterien, die nicht mehr im Fahrzeug einsetzbar sind, werden in der 2nd-Life-Anwendung weiter genutzt. Solche Speicher leisten beispielsweise einen wichtigen Beitrag zur Energiewende, indem sie in Sekundenbruchteilen Strom im öffentlichen Netz aufnehmen oder wieder abgeben. Damit gleichen sie Über- oder Unterspannung aus, die von schwankenden regenerativen Quellen wie Wind oder Sonne verursacht werden, und sorgen so für Netzstabilität.
Recycling ist Teil der Entwicklung
Irgendwann kommt für jede Batterie das endgültige Aus. Dann zeigt sich, was eine nachhaltige Strategie mit einem vollständigen Recyclingkonzept für alle Fahrzeugbauteile Wert ist. Bereits während der Entwicklung werden alle Bauteile und Werkstoffe auf ihre Eignung im Rahmen einer Circular Economy analysiert. Dadurch sind alle Mercedes-Benz Pkw-Modelle zu 85 Prozent stofflich recyclingfähig. Insgesamt 95 Prozent eines Fahrzeugs sind am Ende des Lebenszyklus verwertbar. „Wir verfolgen mit Blick auf die Kreislaufwirtschaft von Batteriesystemen einen ganzheitlichen Ansatz mit drei Kernthemen: Zirkuläres Design, Werterhaltung und das Schließen des Kreislaufs“, sagt Umweltexperte Ruhland. „Das stoffliche Recycling der verwendeten wertvollen Rohstoffe wie Lithium, Nickel, Mangan und Kobalt ist eine Voraussetzung für ein nachhaltiges Geschäftsmodell für die Elektromobilität der Zukunft.“ Mit Blick auf die Laufleistung von Elektrofahrzeugen ist erst in den 2030er-Jahren mit erheblichen Mengen von Akkus für das Recycling zu rechnen. Mercedes-Benz will die Zeit bis dahin nutzen und selbst Know-how für den Wiederverwertungsprozess der kostbaren Materialien entwickeln und sichern. Derzeit evaluiert und plant das Unternehmen den Bau einer Batterierecyclingfabrik im deutschen Kuppenheim. Produktionsstart könnte schon 2023 sein – abhängig von den Gesprächen mit den Behörden.
Grüner Stahl ab 2025
Bei welchen Rohstoffen im fertigen Auto werden in Sachen Nachhaltigkeit die größten Effekte erzielt? Neben den Batterien sind dies Stahl, Aluminium und Kunststoffe. Diese Materialien und Komponenten, die in der Herstellung und Verarbeitung besonders umweltrelevant sind, geht Mercedes-Benz im Rahmen von Ambition 2039 bereits in der Entwicklung und Beschaffung mit besonderem Nachdruck an. Gemeinsam mit den Stahllieferanten verfolgt Mercedes-Benz das Ziel einer grünen Stahllieferkette. „Wir setzen dabei bewusst nicht auf Kompensation, sondern auf die Vermeidung und Reduktion von Emissionen“, betont Stahl-Einkäufer Andre Joao Teixeira Lameira.
Der für den EQS in den Mercedes-Benz Presswerken verarbeitete Stahl besteht zu einem großen Teil aus recyceltem Stahlschrott. Bei der klassischen Hochofenroute verursacht die Herstellung einer Tonne Stahl im Schnitt mehr als zwei Tonnen CO₂. Um mehr als 60 Prozent reduzieren sich diese Emissionen bei Flachstahl der Salzgitter AG, der vollständig aus recyceltem Stahlschrott besteht. Bei Big River Steel, einem US-amerikanischen Stahl-Lieferanten von Mercedes-Benz, vermindert der Einsatz von Stahlschrott und erneuerbaren Energien die CO₂-Emissionen in der Stahlherstellung sogar um mehr als 70 Prozent. Dafür wurde der Lieferant dieses Jahr mit der Daimler Sustainability Recognition ausgezeichnet, einem Nachhaltigkeits-Award für Lieferanten.
Noch weiter geht das schwedische Startup H2 Green Steel, an dem sich Mercedes-Benz als erster Pkw-Hersteller für den Einsatz von CO₂-freiem Stahl in Serienfahrzeugen
Grünes Laden mit Nachhaltigkeit und Transparenz für die Kunden
So reduziert Mercedes-Benz schon heute mit vielen Maßnahmen in Entwicklung, Einkauf und Produktion wirkungsvoll klimarelevante Emissionen und den Verbrauch natürlicher Ressourcen. Allerdings macht die Produktion nur rund die Hälfte des CO₂-Fußabdrucks eines batterieelektrischen Fahrzeugs aus. Die andere Hälfte entsteht in der Nutzungsphase – wenn man den aktuellen EU-Strommix mit seinen Emissionen zugrunde legt. Strom aus erneuerbaren Energien, am besten aus der heimischen Photovoltaikanlage, ist im Lebenszyklus eines Elektroautos also ein signifikanter Faktor, um CO₂-Emissionen zu vermeiden.
Deshalb ermöglicht Mercedes-Benz den Kundinnen und Kunden aller Mercedes-EQ- und Plug-in-Hybrid-Modelle seit März 2021 über Mercedes me Charge das Laden an über 200.000 öffentlichen Ladepunkten in Europa. Green Charging als fester Bestandteil von Mercedes me Charge stellt dabei die Verwendung von Energie aus erneuerbaren Ressourcen sicher. Herkunftsnachweise sorgen dafür, dass für die Ladevorgänge eine äquivalente Strommenge aus erneuerbaren Energien ins Stromnetz eingespeist wird. Der Start von „Green Charging“ in den USA und in Kanada folgte mit dem EQS im August 2021. So ist der Blinker in der vollelektrischen Luxuslimousine von Mercedes-Benz schon gesetzt – in Richtung des Recycling-Kreisverkehrs und einer CO₂-neutralen Zukunft.
¹ Angaben zum Stromverbrauch sind vorläufig und wurden intern nach Maßgabe der Zertifizierungsmethode „NEFZ-Prüfverfahren“ ermittelt. Es liegen bislang weder bestätigte Werte vom TÜV noch eine EG-Typgenehmigung noch eine Konformitätsbescheinigung mit amtlichen Werten vor. Abweichungen zwischen den Angaben und den amtlichen Werten sind möglich.